The Crucial Role Of Hydraulic Systems In Modern Machinery
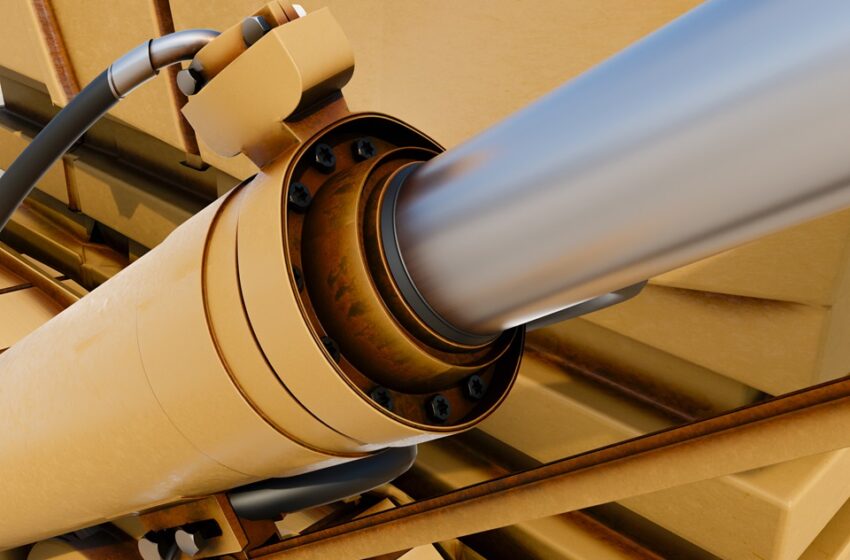
Key Takeaways
- Hydraulic systems are essential for the efficiency and functionality of various industries.
- Understanding different hydraulic components can enhance machinery performance and safety.
- Regular maintenance is crucial for hydraulic systems to prevent common issues and downtime.
Introduction To Hydraulic Systems
Hydraulic systems are integral to modern machinery. These systems utilize fluids to transmit power, enabling precision and control in various applications. Industries spanning from agriculture to aerospace heavily rely on these systems to perform critical functions. The range of hydraulic products available today demonstrates their versatility and importance in industrial settings. They enable machines to perform tasks that require substantial force and precise control, revolutionizing how industries operate and increasing overall productivity.
Hydraulics enable machinery to operate efficiently, handling tasks from lifting heavy loads to precise movements in manufacturing. The underlying technology of these systems is always developing, leading to more reliable and effective solutions that are suited to certain industry requirements. For example, improvements in hydraulic pump technologies have resulted in lower operating costs and greater energy efficiency, which increases the appeal of hydraulic systems to businesses looking to streamline their operations.
Key Components Of Hydraulic Systems
Hydraulic systems comprise several key components, including hydraulic pumps, valves, actuators, and fluid reservoirs. Every part plays a crucial role in ensuring the system operates efficiently and reliably.
Pumps
Pumps are responsible for moving the fluid through the system. They convert mechanical energy into hydraulic energy, thus driving the system. Different kinds of pumps, such as gear pumps, vane pumps, and piston pumps, are appropriate for distinct purposes. The choice of pump can significantly impact the system’s performance and efficiency.
Valves
In order to maintain a safe and reliable system, valves regulate the hydraulic fluid’s flow and pressure. They can direct fluid to specific locations within the system, regulate pressure, and manage the flow rate. These tasks are accomplished by using a variety of valve types, including flow control valves, pressure relief valves, and directional control valves.
Actuators
Actuators transform hydraulic energy back into mechanical energy. Examples include hydraulic cylinders and motors, which perform the mechanical work. Actuators are crucial for converting the energy stored in the hydraulic fluid into actionable force, making them essential for tasks that require lifting, pushing, pulling, or rotating.
Reservoirs
Reservoirs store the hydraulic fluid, helping to cool and filter it, thereby maintaining system efficiency. Additionally, they permit the fluid’s thermal expansion and contraction, guaranteeing that the system functions properly at a range of temperatures. Reservoirs that are designed correctly are essential to preserving the functionality and integrity of hydraulic systems.
Applications In Various Industries
The scope of hydraulic systems across industries is immense. In the construction industry, hydraulics power heavy machinery like excavators and bulldozers. These systems are prized for their ability to manage massive weights and exert significant force with precision. Hydraulic systems can control the movement and force of construction equipment, enabling operators to complete complex tasks efficiently and effectively.
In the manufacturing sector, hydraulic presses and robotic arms rely heavily on these systems for their precise and repeatable motions. Hydraulics enable manufacturing processes to be automated and highly controlled, resulting in increased production rates and improved product quality. Agriculture also benefits, with tractors and harvesters using hydraulic systems to enhance efficiency and productivity. The ability to adjust and control the movement of agricultural machinery enhances planting, cultivating, and harvesting operations.
In aerospace, hydraulics manage critical flight control systems, ensuring safety and reliability. Hydraulic systems are used to operate landing gear, brakes, and flight control surfaces, providing the necessary force and precision required for these critical functions. The continuous development of hydraulic technology underscores its importance in enhancing industrial productivity and precision, making hydraulic systems indispensable across various sectors. For more information, Industry Week provides detailed coverage of the role of hydraulics in modern industry development.
Benefits Of Using Hydraulics
There are numerous advantages to utilizing hydraulic systems, many of which contribute to their widespread use in different industries:
- High Power Density: Hydraulic systems can generate substantial force from compact units, making them ideal for heavy-duty operations. This high power-to-weight ratio allows for the design of more powerful machinery without significantly increasing size and weight.
- Precision and Control: These systems offer precise control over machinery movements, which is crucial in applications requiring delicate and accurate operations. Hydraulic servo systems, for example, can deliver smooth and controlled motion, which is essential in applications like aerospace and robotics.
- Durability: When well-maintained, hydraulic systems have long operational lifespans, proving to be cost-effective over time. Because of their sturdy design, hydraulic parts are less prone to deterioration and require fewer replacements and repairs over time.
Maintaining Hydraulic Systems
Regular maintenance is vital to ensuring the longevity and reliability of hydraulic systems. Essential maintenance practices include:
- Monitoring fluid levels to prevent low fluid conditions, which can damage components. Ensuring the correct fluid type and maintaining the proper volume helps in efficient system operation and prevents cavitation and overheating.
- Inspecting for leaks and addressing them promptly to avoid system inefficiencies and potential failures. Regularly checking hoses, seals, and connections for signs of wear can prevent leaks from causing severe damage to the system.
- Replacing filters regularly to keep the hydraulic fluid clean is vital for preventing component wear and tear. Contaminants in the fluid can lead to clogged valves, worn-out pumps, and other issues that affect system performance.
- Checking component integrity, such as inspecting hoses and seals for any signs of degradation. Maintaining system efficiency and averting unplanned breakdowns are made possible by routine inspection and prompt replacement of worn-out components.
By incorporating these preventive maintenance steps, industries can minimize the risk of sudden breakdowns and extend the lifespan of their hydraulic machinery. Keeping a detailed maintenance log and following the manufacturer’s guidelines for service intervals ensures that the system remains in optimal condition.